Einschneidend anders
Einschneidend anders
Die perfekte Schneidring-Rohrverschraubung ist leckage- und prozesssicher, höchst belastbar und druckbeständig, verhindert systemimmanent Fehlmontagen – und war bislang ausschließlich im Wunschdenken vieler Anwender existent. VOSS Fluid hat nun eine Lösung auf den Markt gebracht, die all diese Vorteile in einem einzigen Schneidringsystem vereint und selbst unerfahrene Monteure zu Präzisionsarbeit befähigt.
Schneidringsysteme sind Sicherheitsgaranten. In hydraulischen Anlagen sorgen sie für die leckagefreie Verbindung von Rohren. So weit zumindest die Theorie. Denn bislang war die prozesssichere Verschraubung immer auch von der Erfahrung und Konzentration des jeweiligen Monteurs abhängig. Diesem wenig zufriedenstellenden Faktum setzt VOSS Fluid nun ein montagesicheres System entgegen: den VOSSRingM mit VOSSRing-Vormontagestutzen. Die patentierte Lösung zur Verbindung von Stahl- und Edelstahlrohren ist einfach in der Handhabung und ermöglicht selbst unerfahrenem oder häufig wechselndem Personal eine punktgenaue Vor- und Endmontage.
Der Ring der Ringe
Basis der intelligenten Lösung ist der VOSSRingM. Mittels optimierter Zweischneidentechnologie gewährleistet er selbst bei dünnwandigen Rohren einen perfekten Einschnitt und einen besonders festen Sitz am Rohr. Der stabile Schneidringquerschnitt sowie weitere geometrische Details garantieren höchste Druck- und dynamische Belastbarkeit. So hält der Ring Drücken von bis zu 800 bar bei einem vierfachen Sicherheitsfaktor problemlos stand. FEM-optimierte Abrundungen am Schneidring vermindern das Risiko von Stutzenbeschädigungen und verhindern wirksam das Mitdrehen der Rohre während der Montage. „Es war unser Anspruch, einen komplett neuen Schneidring zu entwickeln, der in Summe alle relevanten Merkmale einer perfekten Rohrverbindung in sich vereint“, beschreibt Gerd Berghaus, Produktentwickler bei VOSS Fluid, die ehrgeizigen Projektziele. „Daher war es für uns selbstverständlich, auch hinsichtlich des Werkstoffs und Härteverfahrens nach dem Optimum zu forschen.“
Perfekte Materialbeschaffenheit
Im Ergebnis sollte der Schneidring zwei zunächst gegensätzliche Eigenschaften in sich vereinen: eine hohe Festigkeit für den optimalen Rohreinschnitt und um den hohen dynamischen Belastungen standzuhalten, sowie ein weiches und zähes Gefüge, um eine geringe Rückfederung nach der Montage zu ermöglichen. Dafür ließ VOSS einen Sonderwerkstoff mit einer homogenen, feinkörnigen Gefügestruktur entwickeln, der zudem zäh und bruchunempfindlich ist. Das anschließende Härteverfahren verleiht dem VOSSRingM die notwendige dünne, aber besonders harte Randschicht. „Auf diese Weise hatten wir alle Anforderungen erfüllt, die anspruchsvolle Anwender an einen Schneidringwerkstoff stellen“, resümiert Berghaus.
„Was nützt Ihnen der beste Ring, wenn die Fehlerquellen bei der Montage so vielfältig sein können wie die Menschen, die ihn einbauen?“
– Gerd Berghaus | Produktentwickler, VOSS Fluid
Prozesssichere Vormontage mit Anschlagfunktion
Mit der Fertigstellung des VOSSRingM war das Projekt jedoch längst nicht abgeschlossen. „Was nützt Ihnen der beste Ring“, so Produktentwickler Berghaus, „wenn die Fehlerquellen bei der Montage so vielfältig sein können wie die Menschen, die ihn einbauen?“ Um diese Sicherheitslücke konstruktiv zu schließen, entwickelte das Unternehmen ein höchst sicheres Montagewerkzeug: den VOSSRing-Vormontagestutzen. Die Lösung verhindert Montagefehler, indem sie dem Monteur den genauen Endpunkt der Vormontage mittels eines deutlich spürbaren Kraftanstiegs signalisiert. Dieser erwächst aus der integrierten Anschlagfunktion: Ist die Vormontage abgeschlossen, kommt der Stutzen mit einer definierten Anschlagfläche des Rings in Kontakt. Der Montageprozess wird somit am optimalen Punkt beendet – eine Übermontage ist wirksam unterbunden.
Anwenderfreundliche Endmontage
„Wer den VOSSRing-Vormontagestutzen genauer betrachtet, stellt fest, dass er an der Stirnseite etwas länger gearbeitet ist als alle anderen Stutzen“, erläutert Berghaus. „Dieses geometrische Detail bietet bei der Endmontage höchste Leckagesicherheit und zusätzlichen Spielraum für prozesssichere Wiederholmontagen.“ Der neue Stutzen bietet nicht nur ein Höchstmaß an Sicherheit, sondern erleichtert auch die Arbeit der Monteure: Die ausgefeilte Geometrie des Werkzeugs im Rohranschlagbereich verringert den Endmontageweg von 90° auf 30°, damit wird die vom Monteur aufzubringende Arbeit um rund die Hälfte reduziert. Dieser Vorteil kommt insbesondere unter schwierigen Einbaubedingungen wie beispielsweise der Montage über Kopf, in ergonomisch ungünstigen Positionen oder bei besonders engen und kompakten Bauräumen zum Tragen.
Maximale Präzision
Der VOSSRing-Vormontagestutzen besteht aus Hochleistungsstahl, der gegenüber herkömmlichen Standardwerkzeugen nicht verschleißt und zudem noch eine 20-mal längere Werkzeugstandzeit bietet. Diese Eigenschaften machen Verschleißprüfungen komplett überflüssig: Während marktübliche Vormontagestutzen aufgrund des Aufweitens der Konuskontur regelmäßig auf ihre Funktionstauglichkeit geprüft werden müssen, gibt es diese negative Eigenschaft bei dem VOSS Werkzeug nicht. Bei Erreichen der Einsatzgrenze zerbricht der Stutzen – Montagefehler durch Werkzeugverschleiß werden auf diese Weise wirksam unterbunden.
Korrosionsschutz VOSS coat-Black
Dass das neue Schneidringsystem zu 100 Prozent auf Sicherheit, Belastbarkeit und Langlebigkeit ausgelegt ist, zeigt auch die besondere Oberflächengüte des Schneidrings. „Die auf Zink und Nickel basierende Beschichtung VOSS coat-Black trotzt selbst aggressiven Medien und garantiert so auch die kundenseitig gewünschte hohe Korrosionsbeständigkeit“, veranschaulicht Berghaus. So erreicht diese Oberfläche nicht nur die höchste Korrosionsbeständigkeitsklasse K5 nach dem VDMA-Einheitsblatt 24576, sondern überschreitet die geforderten Beständigkeitswerte gegen Weiß- und Rotrost sowohl unter Laborbedingungen als auch im anspruchsvolleren Praxistest deutlich.
Fazit
Das neue Schneidringsystem gewährleistet leckage- und prozesssichere Rohrverbindungen bei höchster Druck- und dynamischer Belastbarkeit. Fehlmontagen werden durch das patentierte Anschlagkonzept sicher unterbunden. Der reduzierte Endmontageweg verringert den benötigten Kraftaufwand und erleichtert die Arbeit der Monteure – auch in engen Bauräumen. Damit ist das System besonders sicher und anwenderfreundlich.
Sichere Rohrverbindung durch Umformsystem VOSSLok40
Sichere Rohrverbindung durch Umformsystem VOSS Lok40
Rohrverbindungen in der chemischen Industrie, der Automobil- oder Energiebranche sollen vor allem eins sein: dicht. Denn treten an diesen sensiblen Stellen Chemikalien, Gase oder Öl aus, kann das ein erhebliches Sicherheitsrisiko darstellen. Zum Verbinden von Edelstahlrohren werden in vielen Bereichen Klemmringe verwendet. Doch diese sind kostenintensiv und führen bei nicht fachgerechter Montage zu Leckagen. Das neue System VOSSLok40, das auf dem in der Hydraulik seit Jahren etablierten Prinzip der Rohrumformung basiert, stellt jetzt eine hochwertige und wirtschaftliche Alternative zum Klemmring dar. Das System punktet nicht nur mit leckagesicheren Verbindungen sondern auch mit seiner prozesssicheren Drehmomentmontage.

Klemmringsysteme sind in vielen Einsatzbereichen etabliert. Voraussetzung für ihre Funktionserfüllung ist allerdings, dass sie richtig angewendet und montiert werden, da sonst Leckagen drohen. Hier kommt es auf eine gute Portion Fingerspitzengefühl des Monteurs an. Mit dem neu entwickelten Umformsystem VOSSLok40 von VOSS Fluid gibt es jetzt erstmalig eineAlternative zur 40° Klemmringverschraubung: Die Lösung gewährleistet eine wirtschaftlich optimierte und dauerhaft sichere Verbindung von Rohren mit höchster Leckagesicherheit. Da die Verschraubungskomponenten in verschiedenen Werkstoffen lieferbar sind und rein metallisch dichten, ist das System für Rohrleitungen zum Transport diverser Medien in verschiedenen Anwendungen einsetzbar: von Wasser über Öl und Gas bis hin zu korrosiven Stoffen.
Clevere Technik aus der Hydraulik
Rohrumformsysteme gelten in der Hydraulik seit Jahren als wegweisend und ersetzen zunehmend andere Verbindungsmöglichkeiten. Der Hersteller VOSS Fluid verfügt über langjährige Erfahrung mit solchen Anwendungen, und überträgt dieses Know-how mit VOSSLok40 jetzt in weitere Branchen. Wie hydraulische Formsysteme besteht auch VOSSLok40 aus drei Komponenten: einer konusförmigen Dicht- und Haltekontur, die an das Rohrende angeformt wird, einer in der Edelstahlausführung standardmäßig versilberten Mutter sowie einem Verschraubungskörper. Mutter und Verschraubungskörper sind so aufeinander abgestimmt, dass beim Anziehen der Mutter die Dichtflächen fest aufeinander gepresst werden. Auch bei hohem Druck wird eine optimale Dichtheit erreicht.
Einfache und sichere Montage
Die Konuskontur am Ende des zu verbindenden Rohres formt der Monteur mit der VOSSLok40 Umformmaschine an. Dies geschieht in drei Schritten. Zunächst wählt der Monteur über Tastendruck an der Maschine den Werkstoff des umzuformenden Rohrs aus und schiebt das Rohr bis zum Anschlag ein. Anschließend spannt die Maschine das Material und formt es um. Dabei ermittelt die Anlage automatisch die erforderliche Kraft und den optimalen Abschaltpunkt. Das schließt eine fehlerhafte Vormontage nahezu aus. Während des Umformprozesses verdrängt die Maschine das Material an der Stirnfläche von innen nach außen und glättet die Rohroberfläche am Dichtradius. Damit verbunden ist eine Entfernung kleinerer Oberflächenfehler am Rohr. Die Endmontage von VOSSLok40 erfolgt in wenigen Schritten und ist über einen Drehmomentschlüssel realisierbar. Der Montagewinkel von 120° führt zu einem deutlich kürzeren Montageweg, verglichen mit einem Winkel von 450° beim Klemmring. Dabei schützt der spürbare Kraftanstieg am Endpunkt vor einer Übermontage, die meist zu Leckagen führt. Auch häufig wechselndes oder ungeübtes Personal erreicht dadurch eine niedrige Fehlerquote und sehr gute Ergebnisse. Ein anschließendes Nachziehen der Verbindung ist jederzeit möglich.
Hohe Dichtigkeit
Selbst bei Nenndrücken bis 700 bar und Temperaturen bis –40 °C sorgt das Formsystem für eine hohe Feinstdichtigkeit. Das hat mehrere Gründe: Die massiv angeformte Kontur weist im Kontaktbereich zur Überwurfmutter eine große Anlagefläche auf, was zu einer sicheren Haltefunktion führt. Die durch Umformung erzeugte hohe Oberflächengüte verringert zusätzlich das Risiko von Leckagen. Darüber hinaus reduziert sich die Anzahl möglicher Leckagepfade um die Hälfte. Sind im Klemmringsystem durch die Außen- und Innenseite der Ringe zwei Leckagepfade vorhanden, lässt die VOSSLok40-Verschraubung nur einen einzigen zu. Dabei wird das Leckagerisiko durch die ideale Kombination von Rohrkontur und Verschraubungsstutzen als auch durch die hohe Anpresskraft der Dichtflächen auf ein Minimum gesenkt. Die überdurchschnittliche Prozesssicherheit in der maschinellen Vormontage und in der Endmontage verhindert schlussendlich Undichtigkeiten durch Anwenderfehler.


Kosteneffizientes System
Neben höchster Dichtheit und Montagefreundlichkeit profitieren Anwender von der Wirtschaftlichkeit der neuen Rohrverbindung. Kostenvorteile ergeben sich insbesondere durch die Prozesssicherheit des Systems, da Leckagen vermieden werden und die damit verbundenen Reklamationen ausbleiben. Der schnelle und automatische Umformprozess mit kurzen Taktzeiten führt zu einem optimierten Arbeitsablauf. Im Ergebnis ist VOSSLok40 damit besonders kosteneffizient und bietet neben den technischen vor allem auch wirtschaftliche Vorteile im Vergleich zu Klemmringverbindungen.
Große Bandbreite an Einsatzmöglichkeiten
Das VOSSLok40 System umfasst verschiedenste Bauformen wie Winkel, T- oder L-Verschraubungen. Die Verschraubungskomponenten sind aus Edelstahl, Stahl oder auf Kundenwunsch aus Sonderwerkstoffen gefertigt und mit unterschiedlichen Außendurchmessern erhältlich. Kombinieren lassen sich diese mit verschiedenen Rohrwerkstoffen wie beispielsweise Edelstahl 1.457, Stahl E235/E355, Aluminium oder CuNiFe-Legierungen (Kupfer-Nickel-Legierungen). Die aus Edelstahl gefertigten VOSSLok40-Komponenten sind gegenüber einer großen Bandbreite von Stoffen rundum korrosionsbeständig. Dadurch ist VOSSLok40 flexibel sehr einsetzbar. Aufgrund der besonderen Geometrie der Rohrkontur ist das System zudem kompatibel mit dem klassischen Klemmring-Stutzen. In dieser Kombination bleibt der Vorteil der Drehmomentmontage erhalten.
Fazit
Die Stärke der VOSSLok40-Verbindung besteht in ihrer hohen Dichtigkeit. Diese resultiert zum einen aus dem Zusammenspiel von Rohrkontur und Verschraubungsstutzen und zum anderen aus der Montagesicherheit des Systems: Der maschinelle Umformprozess führt zu einer sicheren Vormontage und schützt vor Fehlern. Bei der Endmontage signalisiert der spürbare Kraftanstieg den richtigen Sitz der Mutter. Da dieser Arbeitsschritt mit einem Drehmomentschlüssel erfolgen kann, wird eine Übermontage des Verbindungssystems zusätzlich verhindert. Damit leistet VOSSLok40 einen relevanten Beitrag, um enge Toleranzen einzuhalten und kostspieligen Reklamationen vorzubeugen.
Höchste Leckagesicherheit bei hydraulischen Leitungen durch Rohrumformung mit VOSSFormSQR
Höchste Leckagesicherheit bei hydraulischen Leitungen durch Rohrumformung mit VOSSFormSQR
Für die zuverlässige Verbindung von Edelstahl- und Stahlrohren auf und unter Deck bietet VOSS Fluid das Rohrumformsystem VOSSFormSQR. Mit der auch für Marine- und Offshoreanwendungen zertifizierten Lösung erzielt selbst häufig wechselndes Montagepersonal leckage- und prozesssichere Verbindungen. Das System bietet höchsten Korrosionsschutz und hält stärksten Belastungen dauerhaft stand.
Undichte Verbindungsstellen bei Schiffen oder Windparks können schnell zu großen Problemen anwachsen. Damit es erst gar nicht zu einer Leckage sowie zeit- und kostenaufwendigen Lokalisierungs- und Reparaturarbeiten kommt, hat die VOSS Fluid GmbH das Rohrumformsystem VOSSFormSQRentwickelt. Seit über zwölf Jahren ist die Lösung im Feldeinsatz – ohne dass auch nur eine einzige Leckage bekannt wurde. Der Umformprozess gestaltet sich ebenso simpel wie sicher: Im ersten Schritt erhalten handelsübliche Hydraulikrohre an einem Ende eine 24°-Rohrkontur. Die Umformung realisiert die Rohrumformmaschine VOSSForm 100 vollautomatisch. Der Bediener wählt lediglich das passende Werkzeug, schiebt das Rohr gegen die Anschlagplatte und betätigt die Starttaste. Danach formt die Maschine die VOSSFormSQR-Kontur plastisch an das Rohr an. Zum Abschluss der Vormontage wird das umgeformte Rohrende mit einer zusätzlichen Weichdichtung versehen. Dann folgt die Endmontage: Der Monteur setzt mit der Stirnseite des bearbeiteten Rohres auf dem Grund des Verschraubungsstutzens auf. Dies sorgt für einen stabilen Sitz und sicheren Anschlag.
Anschließend zieht er die Mutter an. Da es sich um eine speziell von VOSS Fluid entwickelte SQR-Funktionsmutter mit integriertem Klemmring handelt, wird das Rohr während der Endmontage automatisch radial fest eingespannt. So entsteht eine besonders sichere und hochwertige Verbindung. Der spürbare Kraftanstieg beim Anziehen der Mutter signalisiert dem Monteur zuverlässig das Montageende. Unter- oder Übermontagen sind auf diese Weise praktisch ausgeschlossen. Ein weiterer wichtiger Vorteil: Im Vergleich zu marktüblichen Systemen verringert sich der Montageweg mit dem Rohrumformsystem von VOSS Fluid deutlich. Es werden nahezu identische Ergebnisse wie bei vergleichbaren Dichtkegelverschraubungen erzielt. Dies reduziert den benötigten Kraftaufwand sowie die Montagezeit und kommt vor allem unter schwierigen Einbaubedingungen wie beispielsweise der Montage über Kopf, in ergonomisch ungünstigen Positionen oder bei besonders engen und kompakten Bauräumen zum Tragen.
Höchste Dichtheit und Belastbarkeit
VOSSFormSQR Rohrverschraubungen bieten selbst im Feinbereich eine vollständig dichte Verbindung. Dies ist eine der wichtigsten Voraussetzungen für den Einsatz auf hoher See. Die hohe Dichtheit ist unter anderem auf die zusätzliche Weichdichtung zurückzuführen, die gegenüber einer rein metallischen Abdichtung deutliche Vorteile bietet. Sie verhindert wirksam das Schwitzen der Verbindung – und dies für überdurchschnittlich lange Zeit. Denn das enge Anliegen des Rohres im Stutzengrund, die sogenannte metallische Primärdrosselung, bewirkt eine Dämpfung der Druckwechselbeanspruchung. Dieses marktweit einzigartige Konzept beugt dem Walken oder Ausspülen der Weichdichtung vor und garantiert somit langfristig dichte Verbindungen. Das Rohrverschraubungssystem erfüllt darüber hinaus höchste Ansprüche an Belastbarkeit und Sicherheit. Schließlich müssen Marine- und Offshoreanwendungen aufgrund der stetigen Vibrationen eine besonders hohe Biegewechselfestigkeit aufweisen. Bei VOSSFormSQR sorgen der in der Überwurfmutter befindliche Klemmring und eine tiefe Rohreinspannung für die zuverlässige Resistenz gegen hohe Biegewechselbelastungen: Zum einen wird ein überdurchschnittlich langer Teil des Rohres durch den Verschraubungsstutzen abgestützt.
Zum anderen spannt der Klemmring das Rohr radial am Umfang ein und nimmt dadurch dynamische Belastungen bereits vor dem kritischen Bereich auf. Dies verhindert einen potenziellen Bruch durch Kerbwirkung und erhöht die Druckbelastbarkeit und Bruchsicherheit enorm. Aufgrund der hohen Qualität hält VOSS Fluid die Zulassungen aller Schiffbauklassen der International Association of Classification Societies (IACS). Unter der Dachorganisation IACS sind international anerkannte Klassifikationsgesellschaften zusammengeschlossen, die anwendungsspezifische Anforderungen und Prüfverfahren festlegen und so die internationalen Qualitätsstandards definieren.
Langzeitkorrosionsschutz
Dass VOSSFormSQR zu 100 Prozent auf Sicherheit, Belastbarkeit und Langlebigkeit ausgelegt ist, zeigt auch die besondere Oberflächengüte der Rohrverbindungskomponenten. Die auf Zink und Nickel basierende Beschichtung VOSS coat trotzt selbst aggressiven Medien und garantiert eine besonders hohe Korrosionsbeständigkeit. So erreicht die Oberfläche nicht nur die höchste Korrosionsbeständigkeitsklasse K5 nach dem VDMA-Einheitsblatt 24576, sondern überschreitet die geforderten Beständigkeitswerte gegen Weiß- und Rotrost sowohl unter Laborbedingungen als auch im anspruchsvolleren Praxistest deutlich. Für einige Marine- und Offshoreanwendungen bedeutet dies: Der Oberflächenschutz VOSS coat ist so wirkungsvoll, dass Stahlverrohrungen mit VOSS FluidRohrverschraubungen entgegen der gängigen Praxis teilweise gar nicht mehr überlackiert werden müssen.
Für Anwendungen in Edelstahl kommt das Rohrumformsystem VOSSFormSQRVA zum Einsatz. Alle Verschraubungskomponenten sind in diesem Fall aus Edelstahl gefertigt und weisen komplett identische Produkteigenschaften und Vorteile auf. Höchste Prozess- und Leckagesicherheit, größte Resistenz gegen Belastungen und ausgezeichnete Korrosionsbeständigkeit – diese Merkmale machen das Rohrumformsystem von VOSS Fluid zur optimalen Lösung für die Schiffbau- und die Offshoreindustrie.
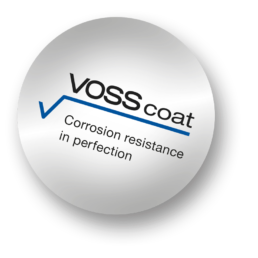
Die unterschätzte Notwendigkeit
Die unterschätzte Notwendigkeit
Rohrverbindungskomponenten sind ein entscheidender Bestandteil von Hydrauliksystemen. Funktionalität und Langlebigkeit hängen unmittelbar von ihnen ab. Unterschätzt wird jedoch die Bedeutung und Auswahl eines hochwertigen Korrosionsschutzes – und das kann Folgen haben.

Wechselnde Temperaturbedingungen und schlagartig auftretende Druckspitzen: Hydrauliksysteme sind höchsten Belastungen ausgesetzt. Unabhängig vom konkreten Einsatzzweck oder von der Abdichtungs- und Belastungsart kommt der Oberflächenbeschichtung von Rohrverbindungskomponenten eine besondere Bedeutung zu. Sie ist Voraussetzung für einen dauerhaften Korrosionsschutz und damit für funktionsbeständige Bauteile. Die Beschichtung dieser Bauteile ist jedoch ein aufwendiger Prozess, bestehend aus einer Vorbehandlung mit Entfetten, Beizen und Dekapieren, der eigentlichen Beschichtung mit einer individuellen Nachbehandlung bis hin zum Passivieren und Auftragen der abschließenden Versiegelung. Um vermeintlich Kosten zu sparen wird auf Hersteller- wie auch auf Kundenseite daher häufig nach der günstigsten Lösung oder entsprechenden Alternativen gesucht. Das kann jedoch ins Auge gehen, vor allem dann, wenn aus einem vermeintlich günstigen Angebot plötzlich billiger Schrott wird. Denn mit einem können die Verwender eines minderwertigen Korrosionsschutzes nicht rechnen: Langlebigkeit. Wer sich aber nicht dauerhaft auf die Funktionsfähigkeit der Bauteile in hydraulischen Systemen verlassen kann, für den wird der Sparzwang schnell zur Milchmädchenrechnung.
Sparen an der falschen Stelle
Vor dieser Einstellung darf also gewarnt werden, denn hier wird an der falschen Stelle gespart. Beispielsweise fällt die Wahl häufig auf eine herkömmliche Zinkbeschichtung. Ein Unternehmen, das auf Qualität setzt, langfristig rechnet und auf eine hohe Prozesssicherheit Wert legt, geht in diesem Bereich keine Kompromisse ein. Der Wipperfürther Hersteller von Rohr- und Schlauchverbindungskomponenten VOSS Fluid setzt bei seinem Korrosionsschutz auf eine Eigenentwicklung auf Basis einer Zink-Nickel-Beschichtung namens VOSS coat. Diese Beschichtung hält selbst aggressiven Medien, wie beispielsweise verschiedensten Düngemitteln, langfristiger stand. Kommen freiliegende Teile beispielsweise in Kontakt mit Mineral- oder Nitratdüngern, kann dies zu verstärkter Korrosion führen. Daher werden sämtliche VOSS-Produkte mit dieser Legierung ausgestattet. Nach der erfolgreichen Markteinführung im Jahr 2007 hat VOSS seinen Korrosionsschutz stetig weiterentwickelt. Die Schichtdicke liegt zwischen 6 bis 15 μm. Bis zu 16 % beträgt der Nickelanteil in der VOSS coat-Oberfläche. Auf eine Basisschicht folgt eine zusätzliche Passivierung und als Finish eine Versiegelung. Unternehmen, die durchgängig auf VOSS Rohrverbindungskomponenten setzen, profitieren daher von einem ausnahmslos hohen Korrosionsschutz. Zudem bildet sich, anders als bei reinen Zinkoberflächen, kein Rot- oder Weißrost.
Zink-Nickel ist nicht gleich Zink-Nickel
Die Besonderheit beim Korrosionsschutz von VOSS ist die Art und Weise, wie das Wipperfürther Unternehmen die hohe Qualität seiner schützenden Beschichtung sicherstellt: mit einer eigens dafür erbauten Galvanik. Statt auf externe Dienstleister zu setzen, beschloss VOSS frühzeitig, in eine eigene Gestell- und Trommelanlage zu investieren. So hat VOSS die Qualitätssicherung und Weiterentwicklung seines Korrosionsschutzes in der eigenen Hand und ist nicht auf Dritte angewiesen, wie Frank Müller, Werksleiter bei VOSS, unterstreicht: „Mit unserer eigenen Galvanik haben wir die Möglichkeit, den Prozess exakt auf jedes Bauteil abzustimmen und je nach Kundenwunsch flexibel zu reagieren. Hier haben wir alles selbst unter Kontrolle, und unsere Kunden wissen, dass sie die Qualität aus einer Hand erhalten.“ In Praxistests, u.a. mit Flüssigdüngermitteln, hat sich die VOSS-eigene Zink-Nickel-Beschichtung bereits mehrfach bewährt, sodass auch sechs Monate nach Testbeginn nur marginale Spuren von Korrosion zu erkennen waren. Damit schneidet VOSS coat im direkten Vergleich mit anderen Zink-Nickel-Oberflächen am besten ab – ein Hinweis darauf, dass die hohe Korrosionsbeständigkeit nicht allein auf die Art der Beschichtung zurückzuführen ist. Für VOSS war dies ein weiteres Argument dafür, in die eigene Galvanik zu investieren.
VOSS beschichtet in eigener Galvanik
Diese Galvanik wurde 2009 im Werk Wipperfürth auf einer Grundfläche von 2.500 m2 errichtet. Diese Investition zahlte sich aus, da die eigens entwickelte Beschichtung VOSS coat für viele Kunden zum wesentlichen Argument wurde, langfristig auf VOSS-Komponenten zu vertrauen. Aufgrund der stetig steigenden Nachfrage nach VOSS-Produkten wurde die Kapazität der Galvanik in diesem Jahr weiter ausgebaut. Die gesamte Anlage ist zweigeschossig errichtet, sodass die Mitarbeiter getrennt von der Chemie arbeiten können – eine Bauweise, die in anderen Galvaniken selten vorzufinden ist. In der unteren Etage, dort wo auch die Gestell- und Trommelanlage bestückt werden, geschehen die komplette Kontrolle und die Prozessmanagement. Auf Monitoren kann das Personal in Echtzeit verfolgen, wo sich welcher Warenträger gerade befindet und wie lange der einzelne Prozessschritt noch dauert. Darüber hinaus können die einzelnen Badparameter, wie beispielsweise die Temperatur, der pH-Wert sowie die Stromparameter, exakt eingesehen und überprüft werden. Die zu galvanisierenden Teile kommen aus der mechanischen Fertigung, in der die Oberflächen innen und außen größtenteils zerspanend bearbeitet werden. Die Komponenten werden in der Gestellanlage sortiert nach Größe und Bauweise einzeln per Hand auf die Gestelle gesteckt.
Rohrverschraubungen, die aufgrund ihrer Größe, ihres Gewichts oder ihrer äußeren Geometrie weniger beschädigungsanfällig sind, kommen in die Trommelanlage. Nach der Bestückung der Gestelle beziehungsweise der Trommeln fahren die Warenträger in die obere Etage, um dort die verschiedenen Galvanikbäder zu durchlaufen, in denen die Komponenten die VOSS coat-Beschichtung erhalten.
Zink und Nickel, die mit einem nahezu hundertprozentigen Reinheitsgehalt als Metall in den Elektrolyt (Lösung von Salzen / Metallsalzen) eingehängt werden, wirken als Anode (Pluspol). Die ebenfalls im Bad befindliche Ware wirkt wie eine Katode (Minuspol). Durch das galvanische Prinzip wandern die Metallionen zum Werkstück und lagern sich darauf ab. Im Obergeschoss geschieht der gesamte Prozessdurchlauf der befüllten Gestelle bzw. Trommeln getrennt voneinander in zwei separaten Anlagen. Über Transportwagen werden die einzelnen Chargen automatisch zu den vom jeweiligen Prozessschritt abhängigen Bädern transportiert und dort eingetaucht.
Labor und Versuchsgalvanik sichern hohe Qualität
Für die richtigen Prozessparameter und die chemische Zusammensetzung der Bäder sorgt das unternehmenseigene Labor, in dem VOSS die Beschichtung permanent überwacht und zudem weiterentwickelt. Zu diesen Optimierungszwecken leistet sich VOSS sogar eine eigene Versuchsgalvanik – eine exakte Kopie der Originalanlage in Miniaturform, bei der alle Prozessschritte nachgestellt und Verbesserungen vor dem Einfließen in die Großserie geprüft werden. Zur Überwachung der Qualität und der gewünschten Funktionsfähigkeit von Weiterentwicklungen gehören auch Salzsprühnebeltests, welche in der hauseigenen Sprühkammer durchgeführt werden. Die beschichteten Bauteile werden dabei unter standardisierten Bedingungen einem Salzsprühnebel ausgesetzt, um deren Korrosionsbeständigkeit nachzuweisen. Neben den Qualitätskontrollen werden im Labor auch permanent Messungen des Abwassers vorgenommen und streng überwacht. Im Zuge des Ausbaus wurde in der oberen Etage eine moderne Zu- und Abluftanlage inklusive Luftwäscher erweitert. Die benötigte Prozesswärme wir durch ein Blockheizkraftwerk im Nebengebäude zur Verfügung gestellt.
Für die nun durchgeführte umfangreiche Kapazitätserweiterung der Galvanik plante VOSS Fluid sehr vorausschauend, da die komplette Ausbaustufe bereits in der eigentlichen Anlagenplanung im Jahr 2008 berücksichtigt wurde. Unter anderem wurden bereits damals die nun benötigten Flächen für die zusätzlichen Bäder an den entsprechenden Stellen freigehalten.
Fazit: Qualität zahlt sich aus
In Korrosionsschutz zu investieren lohnt sich – einerseits für die Kunden (Langlebigkeit) – andererseits für die Hersteller, die wie VOSS Premiumqualität liefern wollen. VOSS coat sticht unter den hochwertigeren Beschichtungen auf Zink-Nickel-Basis noch einmal heraus, da sie einen bis zu 10-mal stärkeren bzw. längeren Schutz als herkömmliche Zinkbeschichtungen liefert. Aufgrund der stetigen Weiterentwicklung erreicht VOSS coat mittlerweile mehr als 2.000 Stunden Korrosionsbeständigkeit – ein stichhaltiges Kriterium für viele Kunden, denn damit übertreffen die Wipperfürther Experten die höchste Korrosionsschutzklasse K5 des VDMA-Einheitsblattes 24576, in dem eine Rotrostbeständigkeit der Oberfläche von mindestens 720 Stunden gefordert wird. VOSS-Rohrverbindungen sind also auch unter realen Bedingungen dauerhaft funktionsfähig und gleichzeitig eine wirtschaftliche Alternative zu Edelstahl. Der Kunde profitiert dadurch von einer deutlich höheren Prozesssicherheit.
Unübertroffen schnell und prozesssicher
Unübertroffen schnell und prozesssicher
In vielen Werkstätten ist es bereits der neue Shootingstar: Das VOSS Vormontagegerät Typ 90 Comfort revolutioniert zurzeit den Markt für die Serienproduktion von Rohrleitungen mit DIN-Verschraubungen. Ein Höchstmaß an Prozesssicherheit in der Schneidringvormontage sowie um bis zu 60 % verkürzte Taktzeiten sind nur zwei der überzeugenden Ergebnisse des Geräteeinsatzes.

Rund um den Globus werden tagtäglich unzählige Kilometer an Rohrleitungen gefertigt, die in unterschiedlichsten Systemen der Stationär- und Mobilhydraulik Einsatz finden. Ihnen gemein ist die Forderung nach sicheren und wirtschaftlichen Rohrverbindungskomponenten. Die Wahl fällt oftmals auf Schneidringsysteme, die – einen Qualitätshersteller vorausgesetzt – bei mustergültiger Montage hohe Leckagesicherheit bieten. Für die korrekte Vormontage sind am Markt diverse Hilfsmittel erhältlich – von Handvormontagestutzen für die Einzelmontage im Schraubstock über Servicemaschinen für die Baustelle bis hin zu Vormontagegeräten für die Serienfertigung. Bei den meisten Montagearten ist der jeweilige Monteur für die korrekte Einstellung und Handhabung zuständig. Genau dieser Sachverhalt birgt allerdings Fehlerpotenzial. Schneidringe können falsch herum aufgesetzt werden. Auch könnten unpassende Schneidringe ausgewählt werden.
Nicht immer werden fehlerhaft vormontierte Leitungen erkannt und ausgemustert; das gilt insbesondere bei häufig wechselndem oder unerfahrenem Personal. Die Folge: Leckagen an Maschinen und Anlagen, die durch Servicetechniker mit teilweise hohem Kosteneinsatz behoben werden müssen – vom Imageschaden ganz zu schweigen. Auch wenn es sich dabei um Ausnahmefälle handelt und qualitativ hochwertige Schneidringsysteme ein sehr hohes Maß an Leckagefreiheit bieten – mit diesem Status quo wollte sich der Verbindungstechnikspezialist VOSS Fluid nicht zufriedengeben. Daher brachte das Unternehmen ein neues Vormontagegerät für die Serienmontage von Schneidringen auf Stahl- und Edelstahlrohre auf den Markt: das Typ 90 Comfort. Die Maschine bietet höchste Prozesssicherheit bei unübertroffen schnellen Taktzeiten.
Fehlmontage ade!
Das massive Plus an Sicherheit bietet das neue Vormontagegerät durch die Kombination von automatisierten Bedien- und Handlingprozessen sowie zuverlässiger Fehlererkennung. Der Monteur rüstet das Vormontagegerät lediglich mit dem zu verarbeitenden Rohr sowie dem passenden, verschleißfest gefertigten VOSS Werkzeug und startet den Vormontageprozess. Ab diesem Zeitpunkt realisiert der Typ 90 Comfort alle weiteren Aufgaben selbsttätig. Zum Einsatz kommt modernste Technik, die zur automatischen Identifizierung von Objekten eingesetzt wird: Im Kolben des Vormontagegeräts befindet sich ein RFID-Lesegerät, zudem sind alle Werkzeuge mit einem RFID-Chip ausgestattet. Sobald die Maschine gerüstet wird, liest sie den Werkzeugchip aus und stellt den benötigten Arbeitsdruck ein. Direkt im Anschluss startet die druck-und wegabhängige Vormontage. So erzielt jeder Monteur mit Leichtigkeit ein präzises und stets reproduzierbares Ergebnis. Durch die hohe Automatisierung sind Bedienfehler selbst bei ständigen Werkzeugwechseln wirksam unterbunden. Allenfalls ein unkorrektes Rüsten der Maschine wäre noch denkbar. In diesen Fällen greift jedoch sofort die integrierte Fehlererkennung: Das Vormontagegerät erkennt zuverlässig alle denkbaren Mängel – beispielsweise einen falsch positionierten oder fehlenden Schneidring – und zeigt sie umgehend auf dem Display an. Ein versehentliches Übersehen der Warnung ist ausgeschlossen. Der Monteur muss die Information manuell bestätigen, um den Fertigungsprozess fortsetzen zu können. Das Ergebnis ist ein Maximum an Prozesssicherheit in der seriellen Schneidringvormontage.
Blitzschnell und hochflexibel
Herausragende Ergebnisse liefert das VOSS-Vormontagegerät jedoch nicht allein im Hinblick auf die Prozesssicherheit. Die Wirtschaftlichkeit des Systemeinsatzes zeigt sich auch in den extrem kurzen Taktzeiten: Bei kleineren Durchmessern liegt die Geschwindigkeit je Schneidringmontage bei ca. 1,8 Sek., beim größten Rohraußendurchmesser von 42 mm bei ca. 2,5 Sek. Im Vergleich zum Vorgängermodell reduzieren VOSS Fluid Kunden ihre Taktzeiten durchschnittlich sogar um über 60 %. Darüber hinaus bietet das Vormontagegerät maximale Flexibilität in der Fertigung. Das durchdachte Maschinendesign erlaubt die problemlose Verarbeitung unterschiedlichster Rohrgeometrien. Auch enge 180°-Bögen und besonders sperrige Leitungsverläufe lassen sich qualitativ hochwertig vormontieren. Möglich macht dies die V-förmige Aussparung am Doppelkolben des Geräts. Bei Bedarf kann der Typ 90 Comfort mithilfe eines Maschinenumbaus durch VOSS Fluid auch für die Vormontage von BV-10 Bördelkegeln und ZAKO Kragenringen eingesetzt werden. Auch bei diesen Rohrverbindungskomponenten gewährleistet das Gerät höchste Prozesssicherheit. Durch die konstante, wegabhängige Montage gehören beispielsweise übermontierte Kegel der Vergangenheit an.
Maßgeschneiderte Systemeinstellung
Jedes Unternehmen, das sich für das neue Vormontagegerät entscheidet, erhält eine komplett auf die individuellen Anforderungen zugeschnittene Maschine. Das betrifft die Anzahl und Zuordnung der verschleißfest gefertigten Werkzeuge ebenso wie optionale Zusatzausstattungen wie Fußschalter oder eine Bedienung für Linkshänder. Die kundenindividuelle Parametrisierung und Kalibrierung der Maschine übernimmt ein VOSS Servicetechniker direkt vor Ort. Anhand von Musterstücken wird bei Bedarf für jedes Rohrmaterial und jeden Durchmesser eine separate Programmierung vorgenommen und Codewort-geschützt gespeichert. Ein USB-Anschluss bietet die Möglichkeit der externen Speicherung und Archivierung, außerdem kann die Programmierung auf diese Weise problemlos auf weitere Geräte überspielt werden. Nachträgliche Anpassungen für Sonderanwendungen sind ebenfalls mühelos umsetzbar. Die frei programmierbare Zähleinrichtung bietet dem Werkstattmeister zudem die Möglichkeit zur statistischen Auswertung; auch Datum und Uhrzeit einer Fehlermeldung sind nachvollziehbar.
Fazit
Das neue Vormontagegerät eignet sich somit vor allem für Unternehmen, die großen Wert auf eine prozesssichere, zügige und wirtschaftliche Vormontage von Schneidringen legen oder häufig Rohre mit engen Radien verarbeiten. Zusammengefasst erzielt das Typ 90 Comfort von VOSS Fluid folgende Ergebnisse:
- ein Höchstmaß an Prozesssicherheit in der Schneidringvormontage
- extrem schnelle Taktzeiten über alle Rohrgrößen
- präzise, reproduzierbare Montageergebnisse
- selbstständige Verhinderung von Fehlmontagen
- Montagen auch bei engsten Rohrbögen
- hohe Werkzeugstandzeiten
Sichere Hydraulik dank hochwertiger Verbindungstechnik
Sichere Hydraulik dank hochwertiger Verbindungstechnik
Hohe Wirkungsgrade, wechselnde Temperaturbedingungen und häufige Lastwechsel – Hydrauliksysteme stationärer und mobiler Arbeitsmaschinen sind stetigen Belastungen ausgesetzt. Um langfristig die größtmögliche Funktionsfähigkeit zu gewährleisten, ist eine korrosionsbeständige und präzise Verbindungstechnik unerlässlich.
Kleine Komponenten mit großer Systemfunktion: Die Prozesssicherheit hydraulischer Verbindungstechnik ist branchenübergreifend ausschlaggebend für den zuverlässigen und wirtschaftlichen Betrieb von modernen Arbeitsmaschinen. Ein zentraler Aspekt ist dabei das Streben nach mehr Energieeffizienz – doch mit den Wirkungsgraden nehmen auch die Belastungen in der Fluidtechnik zu. Damit permanent beanspruchte Anlagen wie Kunststoffspritzgießmaschinen und Großbagger im Bergbau auch unter härteren Bedingungen zuverlässig funktionieren, sind Komponenten entsprechend der Anforderung an die Leckagesicherheit der Verbindungsstelle und mit einem beständigen Korrosionsschutz notwendig. Für den Anwender bedeutet das: Neben der Auswahl systemgerechter Verbindungskomponenten stehen eine fachgerechte Montage sowie die Wahl eines kompetenten Zulieferers im Mittelpunkt.
Die VOSS Fluid GmbH ist Hersteller von Rohrverbindungssystemen und Systempartner des internationalen Maschinenbaus. Das Produktportfolio umfasst Rohrverbindungen für die Stationär- und Mobilhydraulik, darunter Schneidring- und Bördelverschraubungen, Rohrumformsysteme, Flanschverbindungen, Ventile und Zubehör. VOSS Fluid verfügt über langjährige Kompetenz in der Fertigung von Verbindungsteilen gemäß den Anforderungen der Kunden und setzt diese in der Entwicklung der Systemlösungen und der technischen Beratung ihrer Kunden gezielt ein. Das Ergebnis sind gleichbleibend hochwertige Bauteile, ein hoher Korrosionsschutz sowie eine fachgerechte, zeiteffiziente Montierbarkeit der Komponenten und langzeitdichte Hydrauliksysteme.
"Oberflächliche" Qualität mit fachlicher Tiefe
Eine zentrale, qualitative Bedingung ist die Beschichtung der Rohrverbindungen. Sie ist Voraussetzung für einen dauerhaften Korrosionsschutz sowie funktionsbeständige und damit wirtschaftliche Bauteile: VOSS Fluid setzt hierbei für alle Rohrverschraubungen die hauseigene, nachhaltige Zink-Nickel-Beschichtung VOSS coat ein. Diese erfüllt sämtliche Vorgaben der EU-Altauto-Richtlinie, die seit 2007 Chrom-VI-haltige Oberflächen untersagt. Gemeinsam mit unabhängigen Forschungsinstituten und Universitäten, wie der Fachhochschule Aalen, wurde ein Korrosionsschutz entwickelt, der im Vergleich der Basisschichten etwa um ein Zehnfaches besser ist als konventionell eingesetzte Zinkschichten. Anders als reine Zinkoberflächen bildet Zink-Nickel keinen ausgeprägten Weißrost bei der Korrosion, sondern erzeugt lediglich einen leichten Grauschleier.
Die in der EG-Verordnung 1907/2006 aufgeführten Grenzwerte zur Bestimmung der Nickellässigkeit von Produkten, die in direkten und länger andauernden Kontakt mit der Haut kommen, werden um das 50-Fache unterschritten. Im direkten Vergleich der VOSS coat Oberfläche mit einer 2-Euro-Münze wird dieser Grenzwert sogar um das 2.230-Fache unterschritten. Die Oberfläche ist durch den harten Nickelanteil nicht nur umweltverträglich, sondern auch verschleißfester gegenüber mechanischen Belastungen, denen Hydraulikverschraubungen vom Transport über die Montage bis zum Einsatz ausgesetzt sind.
VOSS coat besteht aus einer Zink-Nickel-Basisschicht, die anschließend passiviert und abschließend versiegelt wird. Diese drei Schichten verhindern die Korrosion des Grundwerkstoffs und werten die Verbindungskomponenten nachhaltig auf. Nach dem VDMA-Einheitsblatt 24576 erreicht die Zink-Nickel-Oberfläche die höchste Korrosionsbeständigkeitsklasse K5. Diese bezeichnet die Schutzleistung der Oberfläche, die eine Beständigkeit von mindestens 720 Stunden gegen Rotrost und mindestens 360 Stunden gegen Weißrost nachweist.
Unter Laborbedingungen mit unmontierten Teilen wurde im Salzsprühnebeltest nach DIN EN ISO 9227 sogar eine Korrosionsbeständigkeit von mehr als 2.000 Stunden erreicht. Im Praxistest mit Zufallsware aus der laufenden Produktion wurde nach deren Handling und Montage bewiesen, dass auch bei 1.000 Stunden keine Grundmetallkorrosion auftritt.
Für optimale Montagedrehmomente werden die Reibbeiwerte in der Entwicklung und Produktion für Schneidringverschraubungen laufend verbessert: Dadurch sind diese deutlich geringer als bei anderen Zink-Nickel-Beschichtungen. Je nach Verbindungsbauteil werden ein Gleitmittel und eine partielle Innenbeschichtung eingesetzt, beispielsweise bei Überwurfmuttern. Montagesichere Produktionsprozesse beim Kunden unterstützen erfahrene Anwendungstechniker, welche die Monteure und Instandhalter begleiten – von der Auswahl der systemgerechten Hydraulikverschraubung über Schulungen rund um leckagefreie Verbindungen bis zu regelmäßigen Montageaudits.
Know-how-Vorsprung: In-house-Galvanik
Grundlegende Voraussetzung für die qualitativ hochwertige Beschichtung der Rohrverbindungen ist die werkseigene Galvanik, die einem hohen technologischen Standard sowie den aktuellen Umweltbestimmungen für Wohnmischgebiete entspricht. Sie zählt zu den modernsten Anlagen Europas und ist ideal für die internen Prozessschritte beim Beschichten ausgelegt – dieser hohe Grad der Spezialisierung wäre über Outsourcing nicht erreichbar. Gegenüber dem marktgängigen Beschichten ist der Prozess hinsichtlich der Vermeidung von Bauteilbeschädigungen, Schichtverteilung, Optik und Reibbeiwerten optimiert – die qualitative Reproduzierbarkeit der 6.600 unterschiedlichen Artikel, aus denen sich das noch größere Produktspektrum herleitet, ist stets gewährleistet. Gewicht, Größe, Geometrie – dies sind nur einige der durchschnittlich zwölf Programmparameter, die für jeden Artikel im Produktionssystem hinterlegt sind. Sie sind eine wichtige Voraussetzung, um die unterschiedlichen Verbindungsteile wiederkehrend optimal zu beschichten.
Artikelspezifisch sind die Stromstärke beim Galvanisieren, die Verweildauer im Becken und das Handling klar definiert. Die Gestelle und Körbe, mit denen die Verbindungsteile in der Anlage transportiert werden, sind Eigenentwicklungen. Größere Verbindungsteile mit bis zu 2,5 kg Gewicht und empfindlichen Außengewinden stecken Mitarbeiter manuell auf Gestelle und beugen so potenziellen Gewindebeschädigungen während des Beschichtungsprozesses vor. Bei der Vorbehandlung werden die Artikel per Ultraschall gereinigt, um eventuelle Verschmutzungen der Bohrungen zu entfernen. Kleinere Bauteile werden über Trommeln dem Prozess zugeführt. Die taktweise Befüllung erfolgt über ein Förderband, um die Fallhöhen zu minimieren und prozessbedingte Beschädigungen zu verhindern. Eine deutlich reduzierte Beschichtungszeit schont das Material zusätzlich.
Zur ressourcenschonenden Produktion wird per Online-Analytik und ‑Sensorik der gesamte Galvanikprozess gesteuert und überwacht. Automatische Dosierpumpen sorgen dafür, dass produktspezifisch stets die richtige Menge an Chemikalien zugeführt wird. Die Bäder bleiben so stabil innerhalb der vorgegebenen Prozessgrenzen. Für die gleichmäßige Verteilung der Chemikalien werden diese kontinuierlich in Bewegung gehalten. Nach dem Galvanikprozess werden die Schichtdicke und die Nickeleinbaurate bei jedem Produktionslos kontrolliert. So erfahren die Artikel nachweislich eine gleichmäßige Beschichtung mit VOSS coat und sind dauerhaft gegen Korrosion geschützt.
Seit 2013 wird zudem eine Versuchsgalvanik betrieben, bei der der gesamte Galvanikprozess in Miniaturform abgebildet und ressourcenschonend veränderte Fertigungsparameter simuliert werden können. Neben der Weiterentwicklung von VOSS coat fließen hier auch Optimierungen der internen Prozesse in Bezug auf Effizienz und Nachhaltigkeit mit ein. Anwender profitieren somit von einer zukunftssicheren Oberflächenbeschichtung und kundenspezifischen Systemlösungen.
Qualität von A bis Z
Die Qualität der Produkte, ihre Maßgenauigkeit und damit ihr prozesssicherer Einsatz hängen nicht allein von der Galvanotechnik ab. Der hohe Produktstandard nimmt seinen Anfang bereits bei der Auswahl des Vormaterials, das ausschließlich von auditierten Partnern bezogen wird. Beispielsweise wird per Spektralanalyse im Wareneingang die Zusammensetzung der Werkstoffe sowie mittels eines optischen Profilprojektors, eines Konturmessgeräts oder eines Rautiefenmessers die Geometrie der Waren ermittelt. Auch Härtemessungen und die Prüfung der Elastomere beispielsweise für Dichtungsringe finden hier statt. Eine weitere Besonderheit ist die Maschinenfähigkeitsuntersuchung, die alle Artikel durchlaufen, um eine konstant hohe Produktqualität zu gewährleisten. Mittels statistischer Prozesskontrolle (SPC) wird jedes Produktionslos überwacht – sowohl in der Zerspanung als auch bei der Beschichtung. Während der Zerspanung wird der Verschleiß der Werkzeuge permanent überwacht. Als Schwester der VOSS Automotive, Anbieter von Systemlösungen für die internationale Nutzfahrzeug- und Pkw-Industrie, verfolgt auch VOSS Fluid eine Null-Fehler-Strategie, um den steigenden Anforderungen in der Fluidtechnik gerecht zu werden.
Fazit
Die Prozesssicherheit hydraulischer Systeme in mobilen und stationären Arbeitsmaschinen ist abhängig von der Auswahl der geeigneten Rohrverbindungstechnik für den jeweiligen Einsatzzweck, ihrer Korrosionsbeständigkeit und der fachgerechten Montage. Die Basis legt die VOSS Fluid GmbH mit ihrer Beratungs- und Anwendungskompetenz: Durch die technische Begleitung der Kunden in der Projektierung, dem Engineering und bei der Montage werden montagesichere Produktionsprozesse gewährleistet. Dank der eigens entwickelten Zink-Nickel-Technologie sowie modernen Fertigungs- und Qualitätsstandards erhalten Anwender Rohrverbindungen mit optimalen Montagedrehmomenten und einem hohen Korrosionsschutz. Das Resultat sind langlebige Maschinen sowie ein prozesssicheres und wirtschaftliches Hydrauliksystem.
Ein Plus an Qualität und Wirtschaftlichkeit
Ein Plus an Qualität und Wirtschaftlichkeit
Rohrverbindungskomponenten sind die „Hidden Heroes“ in mobilen und stationären Hydrauliksystemen. Denn die auf den ersten Blick eher unscheinbaren Bauteile sind oft sicherheitsrelevante Systembestandteile. Sie tragen maßgeblich zur Qualität, Effektivität und Langlebigkeit des gesamten Produktes bei. Deutlich wird dies immer dann, wenn es zu Leckagen oder anderen Funktionsbeeinträchtigungen kommt. Genau aus diesem Grund ist die Wahl der richtigen Verbindungstechnik entscheidend. Zu beachten gibt es dabei einiges. Denn trotz ihrer Normierung unterscheiden sich Rohrverbindungskomponenten deutlich in Qualität, Ausführung und Wirtschaftlichkeit.
Dauerhaft leckagefreie Verbindungsstellen erhöhen die Wirtschaftlichkeit und Sicherheit von Hydrauliksystemen und fördern ein positives Produktimage. Voraussetzung ist die optimale Verbindungstechnik für den jeweiligen Anwendungsfall. „Vor der Produktauswahl sollte immer eine konkrete Analyse der wichtigsten Systemparameter stehen“, rät Georg Rempel, Anwendungstechniker bei der VOSS Fluid GmbH. „Entscheidende Faktoren sind beispielsweise Druck, Volumenstrom, Umgebungstemperatur, äußere Einflüsse, Normung und Gesetzgebung sowie die Belastungsart.“ Ist die Entscheidungsbasis definiert, folgt die Auslegung und Auswahl der Verbindungstechnik.
Die Qual der Wahl
Die extrem hohe System- und Typenvielfalt, die der Markt bei Rohrverbindungskomponenten bereithält, bietet für nahezu jeden Anwendungsfall die passende Lösung. Damit stehen Unternehmen allerdings auch vor der Qual der Wahl. Welches System ist langfristig am zuverlässigsten? Und ist dieses auch das wirtschaftlichste? „Der Qualitätsanspruch der Anwender hat sich in den letzten Jahren dramatisch verändert“, berichtet Rempel. „Heute muss es die perfekte Lösung sein – und diese natürlich zum günstigsten Preis.“ Vor diesem Hintergrund haben Normteile an Bedeutung gewonnen. Doch trotz ihrer Standardisierung unterscheiden sie sich erheblich hinsichtlich Qualität und Wirtschaftlichkeit. Wer also Rohrverbindungskomponenten benötigt oder mit der bisherigen Lösung unzufrieden ist, sollte sich die Beratungsleistung eines Qualitätsherstellers zunutze machen. Anwendungstechniker Rempel berichtet: „Meine Erfahrung in der Kundenbetreuung zeigt, dass wir immer spürbar sicherere, haltbarere oder kostengünstigere Alternativen bieten können.“
Wirtschaftlichkeit
Ein wesentliches Kriterium bei der Auswahl des passenden Verbindungssystems ist dessen Wirtschaftlichkeit. Neben dem Einkaufspreis sollten auch die Beschaffungskosten, der Montageaufwand, die Nachhaltigkeit der Dichtfunktion und der Langzeitkorrosionsschutz einbezogen werden. Wer diese Kriterien nicht von Beginn an betrachtet, wird möglicherweise von ungeplant hohen Folgekosten überrascht und muss im schlechtesten Fall sogar einen Systemwechsel in Kauf nehmen. Das heißt konkret: Eine stringente Gesamtkostenbetrachtung kann beispielsweise zur Wahl eines durchgehend weichdichtenden Systems führen, dass im Stückpreis über den Kosten einer rein metallisch dichtenden Lösung liegt. Denn durch das Plus an Prozess- und Leckagesicherheit und die damit gewonnenen wirtschaftlichen Vorteile über den gesamten Maschinenlebenszyklus macht sich die Entscheidung bezahlt.
Sicherheit
Undichte Hydrauliksysteme sind in den meisten Fällen eine direkte Folge von Montagefehlern. Daher raten alle Hersteller, die Bedienungsanleitungen sorgfältig und genau zu beachten. Dennoch bleibt ein gewisses Restrisiko, insbesondere bei Anwendern, die mit unerfahrenem oder häufig wechselndem Personal arbeiten. Abhilfe schaffen hier ausgeklügelte Lösungen, die Fehlmontagen auf ein absolutes Minimum reduzieren oder sogar ausschließen. Das neue Schneidringsystem VOSSRingM mit dazugehörigem VOSSRing-Vormontagestutzen liefert ein solches zusätzliches Plus an Sicherheit. Neben vielen innovativen Systemvorteilen bietet es einen zuverlässigen Schutz vor Montagefehlern. Möglich macht dies ein intelligentes Anschlagkonzept, das dem Monteur den genauen Endpunkt der Vormontage mittels eines deutlich spürbaren Kraftanstiegs signalisiert.
Der Vormontageprozess wird so intuitiv am optimalen Punkt beendet – eine Übermontage ist wirksam unterbunden. Auch bei der späteren Endmontage verhindert das neue Schneidringsystem zuverlässig Fehlmontagen. „Ich rate Entscheidern, die Montagefreundlichkeit bei der Auswahl besonders gründlich zu prüfen“, ergänzt Anwendungstechniker Rempel. „Hierbei sollte der Anwender hinterfragen, welche Werkzeuge, Schulungen und welche Vor-Ort-Unterstützung der Lieferant anbietet. Ein qualitätsorientierter Hersteller wird immer wertvolle Tipps geben, die speziell auf die individuellen Fertigungsprozesse ausgerichtet sind.“
Korrosionsschutz
Unabhängig vom konkreten Einsatzzweck oder von der Abdichtungs- und Belastungsart kommt der Oberflächenbeschichtung der Rohrverbindungskomponenten eine besondere Bedeutung zu. Sie ist Voraussetzung für einen dauerhaften Korrosionsschutz sowie funktionsbeständige und damit wirtschaftliche Bauteile. Diese Faktoren prägen langfristig natürlich auch das Image des Erstausrüsters, da korrosionsbeständige Maschinen für gute Qualität stehen und einen höheren Wiederverkaufswert erzielen. VOSS Fluid entwickelte für seine Produkte eine eigene Zink-Nickel-Beschichtung: VOSS coat. Diese trotzt selbst aggressiven Medien und garantiert so die kundenseitig gewünscht hohe Korrosionsbeständigkeit. Unternehmen, die durchgängig auf VOSS Rohrverbindungskomponenten setzen, profitieren daher von einem ausnahmslos hohen Korrosionsschutz. Denn das Unternehmen stattet alle seine Produkte mit der nachhaltigen Oberfläche aus. „Generell ist natürlich auch eine Verwendung von Bauteilen unterschiedlicher Hersteller möglich“, merkt Anwendungstechniker Rempel an. „Ich rate allerdings davon ab. Unsere Produktlinien sind optimal aufeinander abgestimmt und gewährleisten somit beste Funktion und Qualität.“ Anwendertests zeigen sogar, dass selbst gleiche Oberflächentypen nicht dieselben Eigenschaften besitzen: Die Untersuchung eines führenden deutschen Landmaschinenherstellers ergab, dass keine der getesteten Rohrverbindungskomponenten so korrosionsbeständig gegen aggressive Düngemittel waren wie die mit VOSS coat beschichteten.
Qualität von A bis Z
Die Qualität der Produkte, ihre Maßgenauigkeit und damit ihr prozesssicherer Einsatz sind noch von vielen weiteren Faktoren abhängig. Der hohe Produktstandard nimmt seinen Anfang bereits bei der Auswahl des Vormaterials, das ausschließlich von auditierten Partnern bezogen werden sollte. Qualitätsbewusste Hersteller ermitteln beispielsweise im Wareneingang per Spektralanalyse die Zusammensetzung der Werkstoffe und messen die Geometrie der Waren. Auch Härtemessungen und die Prüfung der Elastomere – beispielsweise für Dichtungsringe – sollten selbstverständlich sein. „Jeder Produktionsschritt wird bei VOSS Fluid durch Qualitätssicherungsmitarbeiter kontrolliert und bei Bedarf sofort optimiert – sowohl in der Zerspanung und der Beschichtung als auch bei der Montage.“ Ziel ist dabei eine besonders hohe Produktqualität und -zuverlässigkeit, um den steigenden Anforderungen in der Fluidtechnik gerecht zu werden. Ein weiterer entscheidender Erfolgsfaktor ist die Logistikkompetenz des Lieferanten. Dieser sollte eine hohe Liefertreue gewährleisten und durch intelligente logistische Dienstleistungen zu verringerten Kosten im C-Teile-Management beitragen. Auch die weltweite Verfügbarkeit des gesamten Katalogprogramms ist von entscheidender Bedeutung. Der Verbindungstechnikspezialist sollte daher rund um den Globus ein engmaschiges Vertriebsnetzwerk betreiben und ständige Versorgungssicherheit gewährleisten.
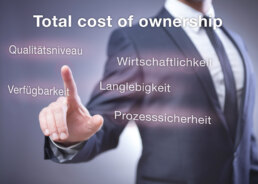
Fazit
Bei der Auswahl hydraulischer Verbindungstechnik stehen Anwender vor der Qual der Wahl. Schlussendlich muss das gesamte Leistungspaket des Herstellers überzeugen. Ein guter Lieferant beherrscht dabei die gesamte Wertschöpfungskette: vom Vormaterial über die Produktion und Oberflächenbeschichtung bis hin zur Logistik. Vor allem ist entscheidend, inwieweit der Lieferant bereit ist, den Anwender aktiv zu unterstützen. Erfahrene Hersteller verfügen über ein breites Wissensspektrum für nahezu jeden Anwendungsfall und bieten individuelle Beratung und maßgeschneiderte Lösungen.
Keine Chance für korrosiven Flüssigdünger
Keine Chance für korrosiven Flüssigdünger
Ein dauerhafter Betrieb von Bodenbearbeitungs- und Sämaschinen ist die Voraussetzung für ein zeiteffizientes und ertragreiches Wirtschaften in der Landwirtschaft. Wichtige Bedingung: Die Maschinen müssen korrosionsbeständig gegenüber Dünger, Regen und Frost sein. Das gilt besonders für funktionskritische Verbindungsteile der Maschinenhydraulik. Wenn das Bauteil nicht optimal auf die Systemanforderungen abgestimmt oder falsch montiert ist, treten hier schnell Leckagen auf.
Die Landwirtschaft ist geprägt von Preisdruck: Betriebe müssen eine hohe Arbeitsproduktivität erreichen – zusätzlich erfordern Umweltauflagen der Europäischen Union ein ressourcenschonendes Bewirtschaften des ländlichen Raums. Einer der führenden Hersteller anforderungsgerechter Maschinen und fortschrittlicher Komponenten für die Bodenbearbeitung, Sätechnik und den Pflanzenschutz ist die Horsch Maschinen GmbH.
Neue Qualitätsstandards in der Hydraulik
Innerhalb der letzten Jahre verzeichnete Horsch einen zunehmenden Bedarf an Düngemaschinen – hier sind die Anforderungen an den Korrosionsschutz der verbauten Teile besonders hoch. „Die Korrosionsbeständigkeit gegen Flüssigdünger und Düngerstaub ist extrem wichtig für unsere Kunden. Sie erwarten einsatzsichere, aber auch optisch einwandfreie Maschinen – und das selbst noch nach Jahren des Betriebs“, betont Thomas Prüll aus der Forschung und Entwicklung bei Horsch. Um Kunden auch in der Fluidtechnik einen zukunftssicheren und gleichbleibend hohen Standard zu gewährleisten, erklärte Horsch die VOSS Fluid GmbH zum Standardzulieferer für die hydraulische Verbindungstechnik. „VOSS Fluid überzeugte uns mit der Zink-Nickel-Beschichtung, die mit ihrem hohen Korrosionsschutz am Markt maßgebend ist“, begründet Thomas Prüll.
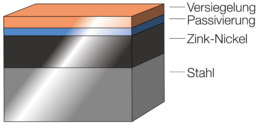
"VOSS Fluid überzeugte uns mit der Zink-Nickel-Beschichtung, die mit ihrem hohen Korrosionsschutz am Markt maßgebend ist."
– Thomas Prüll | Forschung und Entwicklung Hirsch Maschinen GmbH
Ausschlaggebende Argumente für Horsch: VOSS coat übertrifft sogar die höchste Korrosionsschutzklasse K5 des VDMA-Einheitsblattes 24576, in dem eine Rotrostbeständigkeit der Oberfläche von mindestens 720 Stunden gefordert wird. Zudem bildet sich, anders als bei reinen Zinkoberflächen, anstelle von ausgeprägtem Weißrost nur ein leichter, optisch unauffälliger Grauschleier. Mit VOSS coat beschichtete, unmontierte Teile erzielen im Salzsprühnebeltest eine Korrosionsbeständigkeit von mehr als 2.000 Stunden. Aber auch im Praxistest unter realen Bedingungen stellt die Oberfläche ihre hohe Beständigkeit unter Beweis. Dafür durchlief Zufallsware aus der laufenden Produktion die typischen Arbeitsprozesse vom Transport über die Lagerung bis zur Montage mit handelsüblichen Werkzeugen. Trotz mechanischer Beanspruchung zeigte sich an den Verbindungsteilen auch nach 1.000 Stunden keine Grundmetallkorrosion. Um sich der nachhaltigen Eignung auch bezüglich der Anforderungen in der Agrartechnik zu versichern, nahm Horsch VOSS coat genauer unter die Lupe. „Die Ergebnisse aus dem Salzsprühnebeltest sind für uns nur bedingt aussagekräftig“, so Prüll. „Die tatsächlichen Auswirkungen von Montage, Dünger, Temperatur und Feuchtigkeit auf die Korrosionsbeständigkeit zeigen sich erst auf dem Acker.“ Die Bedingungen im Einsatz stellen sogar einen wirkungsvollen Korrosionsschutz auf die Probe: Kommen freiliegende Teile in Kontakt mit Mineral- oder Nitratdüngern, kann dies zu verstärkter Korrosion führen.
Daher prüfen die Entwickler von Horsch in einem eigenen Bewitterungstest seit November 2013, wie sich Verschraubungen verschiedener Hersteller und unterschiedliche Oberflächen über einen längeren Zeitraum verhalten. Um die Praxisbedingungen realistisch nachzubilden, montierte Horsch die Verschraubungen, befestigte sie an einem Gestell und setzte sie der natürlichen Bewitterung aus. Über zwei Monate besprühten die Entwickler die Bauteile jeden Werktag mit einer gängigen und für ihre korrodierende Wirkung bekannten Flüssigdüngerlösung. Den Vergleich traten Bauteile mit A3C-Beschichtung und Zink-Nickel-Oberfläche sowie Verbindungsstücke aus Edelstahl an. Schon nach kurzer Zeit zeigte sich auf den verzinkten, gelbchromatierten Oberflächen und den handelsüblichen Zink-Nickel-Beschichtungen ganzflächig Rotrost. Auf der Verbindungstechnik von VOSS Fluid sind dagegen auch sechs Monate nach Testbeginn nur marginale Spuren von Korrosion zu erkennen. Damit schneidet VOSS coat im direkten Vergleich mit anderen Zink-Nickel-Oberflächen am besten ab – ein Hinweis darauf, dass die hohe Korrosionsbeständigkeit nicht allein auf die Beschichtung zurückzuführen ist. Das Resultat: Die VOSS Rohrverbindungen sind auch unter realen Bedingungen dauerhaft funktionsfähig und gleichzeitig eine wirtschaftliche Alternative zu Edelstahl.
Hohe Fertigungs- und Anwendungskompetenz
Der hohe Korrosionsschutz der Verschraubungen ist begründet in der von VOSS Fluid eigens entwickelten, nachhaltigen Oberflächentechnologie und der langjährigen Erfahrung in der Produktion und Anwendung von Rohrverbindungen. Der Schichtaufbau von VOSS coat ist auf den ersten Blick vergleichbar mit marktüblichen Zink-Nickel-Beschichtungen. Er besteht aus einer Zink-Nickel-Basisschicht, die anschließend passiviert und versiegelt wird. Zentrales Unterscheidungsmerkmal ist die Gestaltung der Beschichtungsprozesse, die der Hersteller aus Wipperfürth kontinuierlich optimiert:
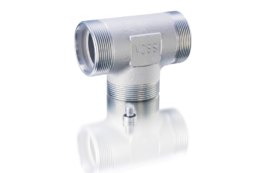
Voraussetzung ist die eigene Galvanik, in der nur Rohrverschraubungen beschichtet werden. So hat sich der Verbindungsexperte auf die effiziente und schonende Reproduzierbarkeit jedes seiner rund 16.000 Artikel spezialisiert – mehr als hundert Millionen Teile laufen jährlich durch die Galvanik. Dank der eigens für jedes Produkt hinterlegten Prozessparameter erreicht VOSS hochwertige Ergebnisse hinsichtlich einer gleichmäßigen Schichtverteilung, der Optik und der Reibbeiwerte. Schulungen zur leckagefreien Montage der Verbindungstechnik gewährleisten Horsch zusätzlich einen prozesssicheren Einbau ins Hydrauliksystem. Reklamationen in Bezug auf die Verschraubung gehören seit dem Wechsel zu VOSS Fluid der Vergangenheit an.
In der Verbindung liegt die Kraft
In der Verbindung liegt die Kraft
Was haben Medizinprodukte und Autos gemeinsam? Beides sind Hightechentwicklungen, die ohne hochpräzise gefertigte Bauteile nicht funktionieren. Möglich ist eine solch genaue Bearbeitung mit den Werkzeugmaschinen der GROB-Gruppe. Bei der spanenden Fertigung wirken extrem hohe Kräfte auf die Werkstücke ein. Sämtliche Vorrichtungen für die Werkzeug- und Werkstückspannungen werden daher mit einer ausgefeilten Hydraulik betrieben. Bei den Hydraulikverbindungen vertraut GROB auf das Rohrumformsystem VOSSFormSQR in Kombination mit der prozesssicheren Umformmaschine VOSSForm 100. Darüber hinaus setzt das Unternehmen weitere Komponenten von VOSS Fluid ein, wie leckagesichere Schneidringverschraubungen.
Der Name GROB steht international für Werkzeugmaschinen höchster Präzision. In der Automobilindustrie, im Flugzeugbau, in der Medizintechnik und in einer Reihe weiterer Branchen genießt das Familienunternehmen mit Sitz in Mindelheim großes Vertrauen. Das Produktportfolio gliedert sich in die Bereiche Systemmaschinen, Universalmaschinen für die spanende Bearbeitung, Anlagen für die Elektromobilität, komplette Montageanlagen, bestehend aus modular aufgebauten Bearbeitungszentren und Sondermaschinen, sowie den Bereich neue Technologien. Weltweit erwirtschaftet die GROB-Gruppe mit knapp 6.000 Mitarbeitern auf vier Kontinenten einen Umsatz von rund 1,3 Mrd. Euro. „Wir stellen hohe Anforderungen an uns selbst und haben den Anspruch, die Nummer 1 zu sein. Das erfordert ständige technische Innovationen. Genau das Gleiche erwarten wir auch von unseren Zulieferern“, erläutert Anton Kuhn, Abteilungsleiter Fluid-Konstruktion bei GROB.
Universalmaschinen von GROB
GROB 5-Achs Universalmaschinen lassen sich in den unterschiedlichsten Bereichen einsetzen – wie beispielsweise dem Formen- und Prototypenbau mit anspruchsvollen, hochgenauen Geometrien mit Raumschrägen und Raumbohrungen. Die Werkzeugmaschinen arbeiten auf einen tausendstel Millimeter genau. Eine solch exakte Bearbeitung setzt voraus, dass die Werkstücke in komplexen Spannvorrichtungen positioniert und fixiert werden. Dabei kommt der Hydraulik eine besondere Bedeutung zu. Sie hat die Aufgabe, Werkzeuge zu spannen und Gewichte auszugleichen. Außerdem sorgt sie für die Klemmung von Achsen und Spindeln. In der Regel wirken bis zu 120 bar auf die Hydraulikverbindungen, bei Druckspitzen vereinzelt sogar bis zu 300 bar. Rund 70 bis 100 m Hydraulikleitung sind in den Werkzeugmaschinen der G-Reihe verbaut, hinzu kommen unzählige Verbindungen. Gemäß den von GROB definierten Qualitätsstandards müssen die Verbindungselemente zwischen den einzelnen Hydraulikrohren höchste Leckagesicherheit aufweisen. „Die Hydraulik ist ein sensibler Bestandteil unserer Werkzeugmaschinen, denn hydraulische Antriebe sorgen für höchste Präzision bei den Werkzeugbewegungen. Daher muss die Verbindungstechnik zuverlässig und dauerhaft leckagefrei sein“, betont Kuhn. Neben der Leckagefreiheit sind eine einfache Handhabung und ein attraktives Preis-Leistungs-Verhältnis weitere Anforderungen, die GROB an seine Lieferanten von Hydraulikverbindungen stellt.
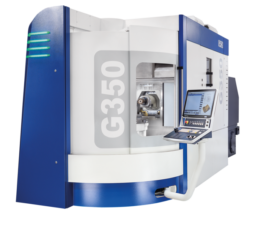
Einfach leckagefrei
Mehrheitlich setzt GROB die Verbindungslösung VOSSFormSQR ein. Neben der Qualität war die einfache Handhabung von VOSSFormSQR ein ausschlaggebender Grund. Um eine sichere Verbindung zu erzeugen, sind nur wenige Arbeitsschritte erforderlich: Zunächst formt die Umformmaschine VOSSForm 100 binnen wenigen Sekunden an das Ende eines Hydraulikrohres eine 24° Rohrkontur an. Dazu muss das Rohrende bis zur Anschlagplatte in die Maschine geschoben werden. Da ein Innendorn am Ende des Stauchkopfes die Einschnürung des Rohres verhindert, bleibt der Rohrinnendurchmesser vollständig erhalten und Druckverluste durch Einwölbungen werden verhindert.
Zusammen mit einer Weichdichtung aus FKM und einer spezifischen SQR-Funktionsmutter entsteht eine einfache und hochwertige Verbindung. Besonders die Montagesicherheit durch den Schutz vor Übermontage ist für GROB ein entscheidender Vorteil des Systems: Bei der Endmontage schlägt die Stirnseite des mit VOSSFormSQR umgeformten Rohrendes gegen den Stutzengrund im Verschraubungskörper. Beim Anzug der Funktionsmutter werden diese Komponenten fest miteinander verspannt, wobei ein spürbarer Kraftanstieg dem Monteur das Erreichen des Montageendes signalisiert. „Ein Großteil aller auftretenden Leckagen entsteht durch falsche Montage. Mit VOSSFormSQR reduzieren wir dieses Risiko entscheidend. Deshalb ist diese Technik unserer Ansicht nach die sicherste und beste Verbindung. Auch unsere Mitarbeiter sind mit dem System zufrieden“, sagt Kuhn. Weltweit hat GROB zwölf VOSSForm 100 Umformmaschinen im Einsatz.
Weichdichtende Schneidringe
Ergänzend zur Rohrumformung mit VOSSForm 100 setzt das international agierende Familienunternehmen auch den weichdichtenden Schneidring ES-4 aus dem Hause VOSS ein. Diesen verbaut GROB insbesondere in den Systemmaschinen für die Automobilindustrie. Das Funktionsprinzip basiert auf einer Zwei-Schneiden-Technologie mit zwei zusätzlichen Weichdichtungen. Die beiden Weichdichtungen sind eine Besonderheit des ES-4: Mithilfe der vollständig spaltfrei gekammerten Weichdichtung garantiert der ES-4 auch bei einem eventuellen Nachlassen der metallischen Dichtung eine trockene und schwitzfreie Verbindung. Selbst Vibrationen hält die Verbindung auf diese Weise stand. Die spaltfreie Kammerung der Dichtung erreicht der Anwender durch die Blockmontage. Diese vermeidet, dass der Ring zu tief einschneidet – eine Übermontage wird somit verhindert.
Service und Schulungen
An seinem Partner VOSS Fluid schätzt GROB nicht nur die hohe Qualität der Produkt und deren einfache und sichere Handhabung, sondern auch den Service. „VOSS Fluid ist ein agiles Unternehmen und kundennah aufgestellt“, beschreibt Kuhn. Um die geforderten kurzen Reaktionszeiten zu gewährleisten, hält VOSS Fluid zusammen mit ihrem Premium-Vertriebs- und -Servicepartner, der Fritz Stiefel GmbH, jeweils einen Teil des benötigten Materials bereit. GROB profitiert nicht nur von hoher Termin- und Liefertreue, sondern auch von Produkt- und Montageschulungen. Gemeinsam mit ihrem Vertriebs- und Servicepartner trainiert VOSS Fluid die Monteure des Maschinenbauers regelmäßig in der korrekten Anwendung der VOSS Lösungen.
Kanban-Service durch die Stiefel GmbH
Seit mehr als 13 Jahren leistet der VOSS Fluid Partner Stiefel für GROB einen Kanban-Service. Dieser ist über ein klassisches Zwei-Kisten-System mit einer definierten Mindestfüllmenge organisiert. Dreimal pro Woche tauscht die Stiefel GmbH die Behälter aus. Einmal pro Woche ist zudem ein Fachmann aus dem Bereich der Hydrauliktechnik vor Ort und unterstützt GROB in allen Fragen zu den VOSS Lösungen. „Seit dreizehn Jahren arbeiten wir mit VOSS und Stiefel zusammen. Seitdem sind wir sehr zufrieden mit der Produktqualität und dem Service, den wir durch diese Partnerschaft erhalten. Wir wünschen uns, dass das in Zukunft so bleibt“, resümiert Kuhn.
Kleiner Ring – große Aufgabe
Kleiner Ring – große Aufgabe
In weniger als einer Minute nimmt das Spezialfahrzeug Phoenix der Goldhofer Unternehmensgruppe ein Flugzeug auf und transportiert es bei Bedarf gleich mehrere Kilometer über die Rollbahn bis ans Ziel. Dabei können auch Vibrationen entstehen, die eine maximal belastbare Rohrverbindungstechnik erfordern. Bei seinem neuen Flugzeugschlepper vertraut Goldhofer daher ausschließlich auf Komponenten von VOSS Fluid wie leckagesichere, weichdichtende Schneidringe in Kombination mit einem speziellen Vormontagegerät. Eine besondere Bedeutung im Einsatz bei Wind und Wetter und gegen aggressive Enteisungsmittel im Winter kommt zudem dem langzeitsicheren Korrosionsschutz durch die Zink-Nickel-Beschichtung VOSS coat zu.
Der Name Goldhofer steht für robuste und intelligente Transportlösungen im Schwerlast- und Spezialtransport – auf der Straße, Offroad und am Flughafen. Weit über 35.000 Fahrzeuge lieferte das Unternehmen weltweit in mehr als 160 Länder, darunter auch über 6.000 Flugzeugschlepper. Ohne sie wäre der Airport-Betrieb undenkbar, denn auch das modernste Flugzeug kann eines nicht: den Rückwärtsgang einlegen. Genau an dieser Stelle übernehmen die Goldhofer-Fahrzeuge, die die Maschinen exakt in die gewünschte Start- oder Parkposition ziehen und schieben. Brandneu auf dem Markt ist der AST-2P/X, kurz: Phoenix. Die vierte Generation der stangenlosen Flugzeugschlepper ist in der Lage, mehr als 80 Prozent aller weltweit eingesetzten Flugzeuge zu bewegen.
Dazu zählen unter anderem die neue A350 von Airbus sowie die in der Entwicklung befindliche B777X von Boeing. „Geniale Lösungen sind immer einfach. Aber einfache Lösungen zu entwickeln, ist eine große Herausforderung“, bringt es Stefan Fuchs, Vorstandsvorsitzender der Goldhofer Aktiengesellschaft, auf den Punkt. „Mit dem Phoenix wollten wir weg vom allgemeinen Trend des Over-Engineerings. Daher haben wir uns auf das Wesentliche konzentriert und uns auf höchste Verfügbarkeit, verlässliche Technik und minimalen Wartungsaufwand fokussiert.“ Das Ergebnis ist ein komplett neues, kompaktes und modulares Fahrzeugkonzept, das in Punkto Antrieb, Motor, Bremskraft und vielen weiteren Bereichen neue Maßstäbe in Funktionalität und Kundennutzen setzt.
Beispiel Aufnahmevorrichtung
Nur ein wahrer Kraftprotz kann ein voll besetztes und voll betanktes Flugzeug bewegen. Der Phoenix leistet dies, indem er das Bugrad des Flugzeuges mit den Schwenkarmen seiner Aufnahmevorrichtung umschließt, spannt und anhebt. In dieser Position zieht der Schlepper die Maschine bei Bedarf kilometerweit in der auf Flughafenarealen zugelassenen Höchstgeschwindigkeit von 32 km/h. Um das Flugzeug sicher aufzunehmen benötigt der Phoenix weniger als eine Minute – was unter Flugzugschleppern einer Rekordzeit entspricht. Doch Goldhofer ging es bei der Entwicklungsphase nicht nur um eine optimale Performance. Unter der Maßgabe des Lean-Design-Gedankens wurde die Aufnahmevorrichtung komplett neu gestaltet. Waren bei den Vorgängermodellen beispielsweise noch 14 Hydraulikzylinder im Einsatz, kommt der AST-2P/X mit acht Zylindern aus. Das übersichtliche Hydraulikschema bietet freien Zugang zu allen entscheidenden Wartungspunkten. Und entgegen dem Trend, Hydraulikrohre zunehmend durch Schläuche auszutauschen, setzt Goldhofer auf Hartverrohrung.
„Wir verzichten weitgehend auf Schläuche, weil diese sehr wartungsintensiv sind“, erläutert CEO Fuchs. „Rohre hingegen müssen nur zu Beginn vernünftig montiert werden. In Kombination mit zuverlässiger Verbindungstechnik entstehen wartungsarme, leckagefreie Systeme, die über die gesamte Lifetime-Performance unserer Fahrzeuge zuverlässig arbeiten.“ Voraussetzung ist der Einsatz qualitativ hochwertiger Komponenten. Eine besondere Rolle innerhalb des Hydrauliksystems übernimmt dabei die Rohrverbindungstechnik. Hier setzt der Spezialist für Spezialtransportfahrzeuge auf die weichdichtenden Schneidringe ES-4 der VOSS Fluid GmbH. „Unserer Entscheidung für diese Technologie gingen zahlreiche Tests und Eignungsprüfungen voraus“, berichtet Fuchs. „Schließlich ist eine perfekte Hydraulik von Flugzeugschleppern das wichtigste Argument für Funktionalität und Langlebigkeit.“
Hohe Dauerfestigkeit
Die weichdichtenden Schneidringe ES-4 bieten selbst bei kontinuierlicher dynamischer Belastung die von Goldhofer geforderte dauerhafte und sichere Rohrhaltung sowie höchste Leckagesicherheit. Sie kommen an diversen Hydraulikverbindungsstellen des neuen Flugzeugschleppers zum Einsatz, unter anderem am Vormontageschild, einem entscheidenden Bauteil der Bugrad-Aufnahmeeinrichtung. Das Plus an Leckage- und Prozesssicherheit des Schneidrings ist unter anderem auf die ausgeklügelte Zweischneidentechnologie sowie die beiden integrierten Weichdichtungen zurückzuführen. Der Blockanschlag des Systems sorgt darüber hinaus für Übermontageschutz. Durch die Verteilung der Belastung auf zwei Schneiden erhält die Verbindung eine besonders hohe Dauerfestigkeit: Während die erste Schneide für den sicheren Halt des Rohres sorgt, optimiert die zweite Schneide die Ausreißsicherheit bei Druckschlägen und reduziert zudem die Gefahr von Leckagen auf ein absolutes Minimum. Der im Körper des Schneidrings integrierte Federeffekt verhindert zusätzlich Nachsetzerscheinungen, die durch Vibrationen entstehen könnten. Selbst lang anhaltende Vibrationen, wie sie beim kilometerlangen Abschleppen eines Flugzeuges entstehen können, wird auf diese Weise wirksam standgehalten.
Im Sekundärbereich des Schneidrings befinden sich zwei vollgekammerte Weichdichtungen aus FPM. Sie dichten die beiden möglichen Leckagewege zum Rohr und zum Stutzen zusätzlich ab für den Fall, dass Hydraulikflüssigkeit die metallische Dichtung überwinden sollte. Eine besonders hohe Langzeitstabilität der Elastomere gewährleistet VOSS Fluid sowohl durch die Materialauswahl als auch durch die geschützte Platzierung der gekammerten Weichdichtungen innerhalb des Schneidrings.
Prozesssichere Montage
Bezüglich der Vor- und Endmontage forderte Goldhofer maximale Prozesssicherheit. Nicht zuletzt, weil sich statistisch mehr als 90 Prozent aller Leckagen von Verschraubungen auf Fehlmontagen zurückführen lassen. Der Spezialist für Spezialtransportfahrzeuge entschied sich daher für die Anschaffung mehrerer Vormontagegeräte der neusten Generation: Der Typ 90 Comfort von VOSS Fluid arbeitet mit Fehlererkennung und automatischer Druckeinstellung. So werden fehlende oder falsch eingelegte Schneidringe schon vor der Montage identifiziert sowie Über- und Untermontagen wirksam unterbunden.
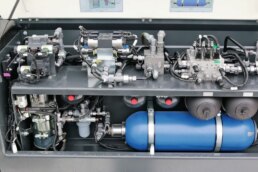
Die Monteure bei Goldhofer rüsten das Vormontagegerät lediglich mit dem passenden verschleißfesten VOSS Werkzeug, das standardmäßig mit einem RFID-Chip ausgestattet ist. Das ins Typ 90 Comfort integrierte RFID-Lesegerät liest den Chip aus und stellt die entsprechenden Montageparameter automatisch ein. Direkt im Anschluss beginnt die prozesssichere und zudem äußerst zügige Vormontage. Auch die Endmontage ist sicher gestaltet, da der ES-4 Schneidring auf Blockanschlag montiert wird. Der deutliche Kraftanstieg signalisiert dem Monteur eindeutig den Endpunkt der Montage. Zum Abschluss markiert der Goldhofer-Mitarbeiter die Verschraubung mit einem gelben Kreuz – jedes Mal ein Zeichen für eine weitere perfekte Verbindung.
Langzeitkorrosionsschutz
Da Flugzeugschlepper bei allen Wetterbedingungen zum Einsatz kommen und im Winter sogar besonders aggressiven Enteisungsmitteln ausgesetzt sind, waren die Forderungen von Goldhofer auch im Hinblick auf den Korrosionsschutz kompromisslos. „Alle unsere Systembauteile sind mit höchstem Korrosionsschutz ausgelegt. Das muß natürlich auch für die Rohrverschraubungen gelten“, berichtet Fuchs. „Damit ist das gesamte System widerstandsfähiger gegenüber mechanischer Beanspruchung und gegenüber aggressiven Medien.“ Für den neuen Phoenix bedeutet dies: Sämtliche Hydraulikleitungen sind galvanisch verzinkt und erhalten eine zusätzliche organische Schutzschicht. Und auch die Rohrverschraubungen verfügen über einen besonderen Zink-Nickel-Oberflächenschutz. Im Fall der ES-4-Schneidringe ist dies der Langzeitkorrosionsschutz VOSS coat. Er erreicht nicht nur die höchste Korrosionsbeständigkeitsklasse K5 nach dem VDMA-Einheitsblatt 24576, sondern überschreitet ebenfalls die geforderten Beständigkeitswerte gegen Weiß- und Rotrost deutlich. „Die ES-4 Schneidringe erfüllen unsere hohen Erwartungen zu einhundert Prozent“, resümiert CEO Fuchs zufrieden. „In VOSS Fluid haben wir einen absolut qualitätsorientierten Partner, auf den wir uns jederzeit verlassen können.“